BRICK RED
HAMBURG‘S ARCHITECTURAL HERITAGE –
A TRIBUTE TO THE HUMBLE BRICK
Hamburg maintained its love for brick-work over centuries. The love affair began after the Great Fire in 1842, which destroyed about 20 percent of all buildings in Hamburg. Bricks became a highly sought-after non-flammable construction material, and inspired some impressive pieces of architecture. When UNESCO granted world heritage status in 2015 to the Speicherstadt and Kontor-viertel districts and the Chilehaus building, an icon of Brick Expressionism by Fritz Höger, this love was rekindled. A trail of red brick façades blazes through the city and makes up a large share of its architectural heritage.
Until today, bricks remain a favourite element of local façade design both for residential and commercial buildings. Hamburg‘s identity is founded on the varied shades of red of the brick façades and the sturdiness of the fired stone. Not only are bricks a defining stylistic element and extremely weather-hardy, their distinctive colouring also tells the story of what they are made of and how the were fired: They consist of clay that is processed, formed and fired in a manufacturing process.
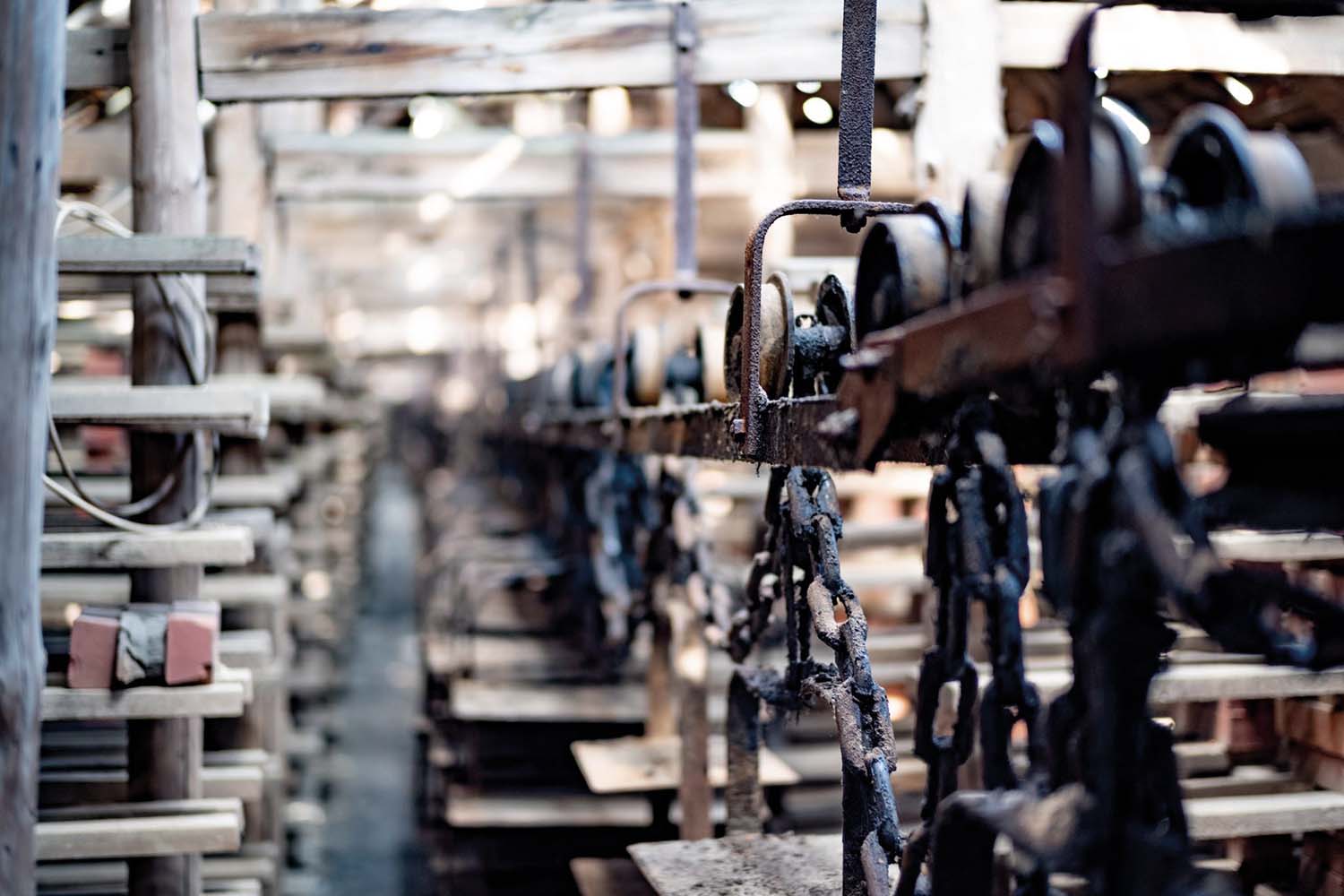
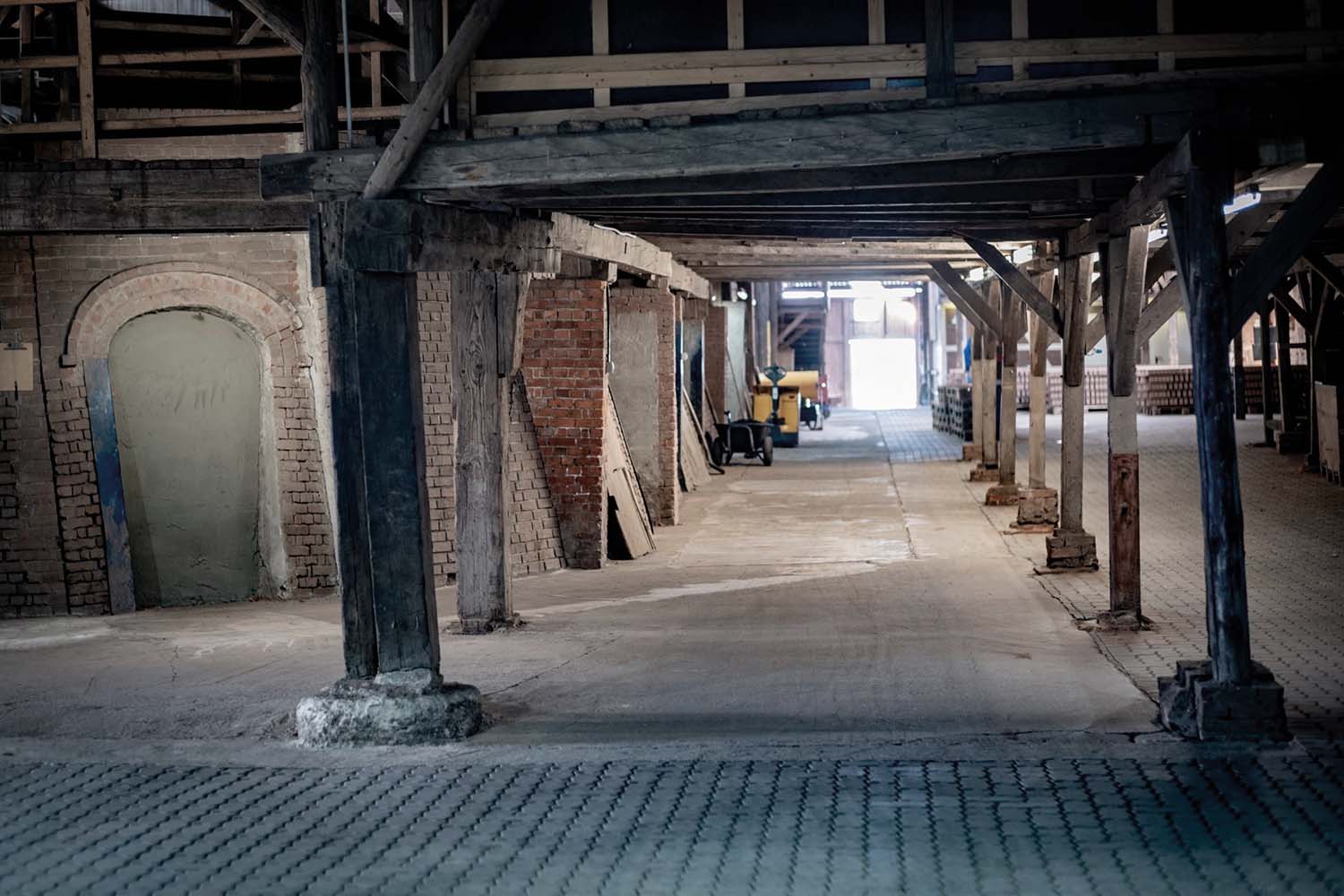
The traditional firing method in a ring kiln makes each brick unique. The bricks used for the Tichelhaus are manufactured the old-fashioned way: In a hand-fired ring kiln.
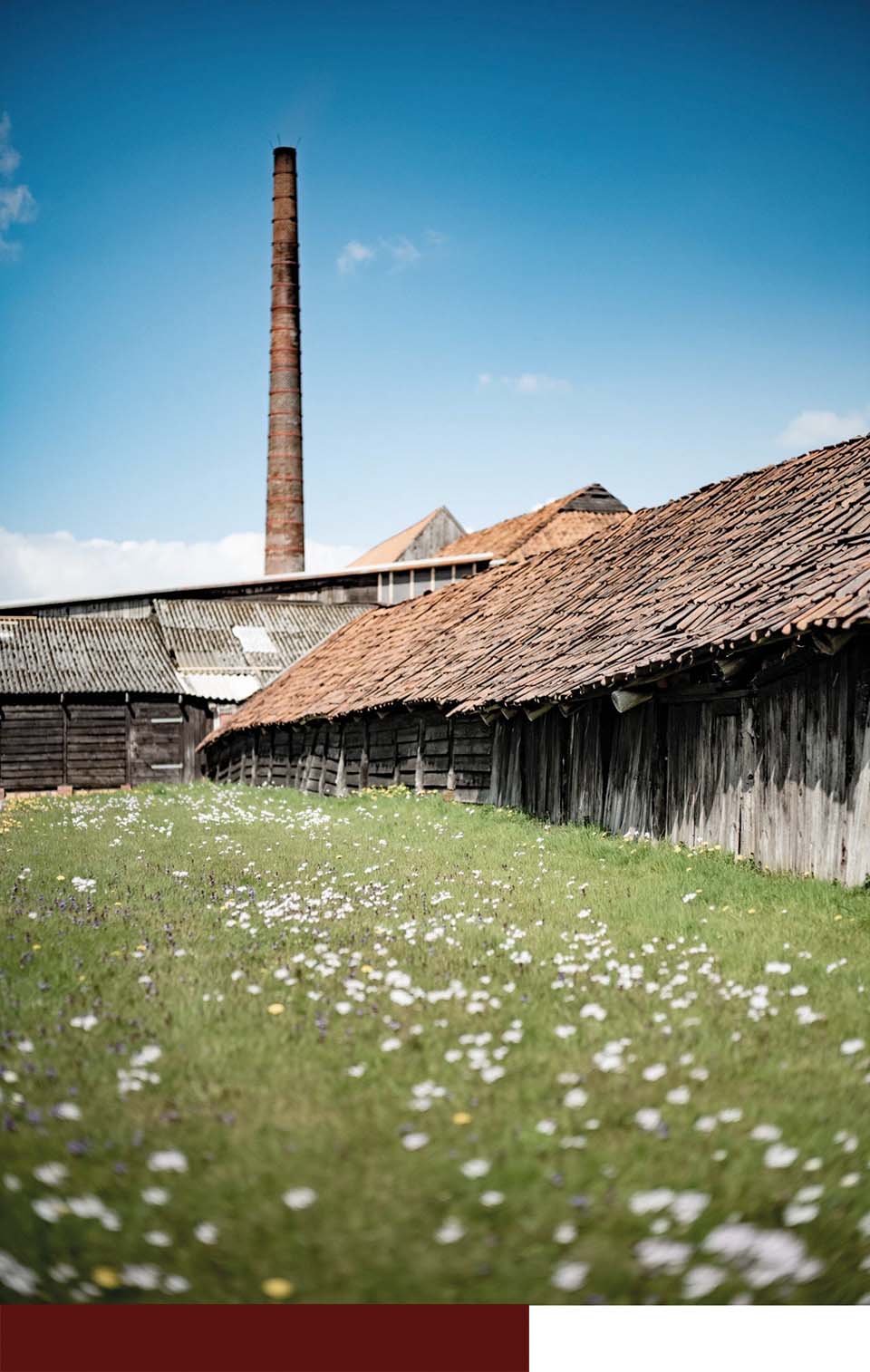
BRICKS FROM THE REGION
Clay from the Elbmarsch region provides the raw material for the Tichelhaus bricks. Manufacturer Rusch burns the bricks in a traditional ring kiln. The brickyard, founded in 1881, is the last of over 100 that existed between Hamburg and Cuxhaven in the second half of the 19th century. The skill and knowledge required for processing the natural material is passed on through generati-ons, and each of the hand-made bricks is unique. Together, they create the vibrant feel of the Tichelhaus façade – a façade made of a natural material coming straight from the Elbe river‘s glacial valley.